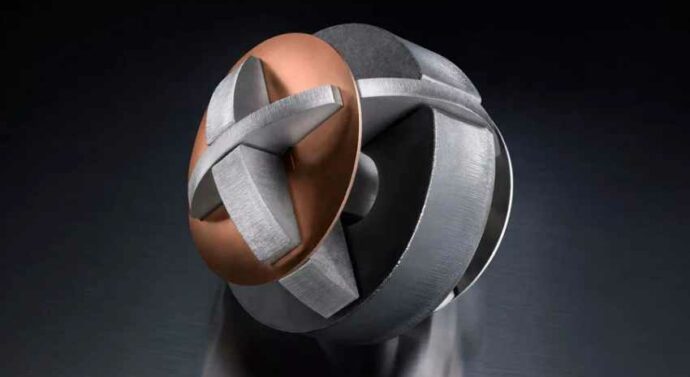
Рекомендации по проектированию деталей для лазерной резки
Лазерные технологии, Новости науки и техники, Промышленные лазеры 01.09.2023 Комментарии к записи Рекомендации по проектированию деталей для лазерной резки отключеныТребования к кромке, точки прожига и толщина материала — это лишь некоторые из факторов, которые следует учитывать.
Несмотря на то, что лазерная резка была неотъемлемой частью производства металла в течение последних 20 лет, она все еще может быть новой для начинающих производителей листового металла и пластин. Эти советы по дизайну помогут им освоиться.
№ 1: Лазер меняет материал
Любой, кто использует лазер для обработки деталей, должен понимать, что источник света высокой интенсивности, используемый для генерации лазерного луча, настолько горячий, что плавит металл за миллисекунду. Поэтому любая деталь, обработанная лазером, подвергается сильному нагреву и имеет зону термического влияния по краю разреза.
Почти для всех производителей эта зона термического влияния не является проблемой, но в некоторых областях, например в аэронавтике, она может стать серьезной проблемой. Критически важные детали для этих отраслей часто не вырезаются лазером, поскольку инженеры-конструкторы не могут рисковать тем, что в металле образуются микротрещины, которые могут создать проблемы в будущем.
№ 2: Следите за сужением
Все детали, обработанные лазером, имеют некоторую конусность, поскольку сфокусированный лазерный луч не идеально прямой, а имеет форму песочных часов. В тонком материале конусность настолько минимальна, что не является проблемой. Конусность начинает проявляться в материале толщиной 0,50 дюйма и толще.
Производители, обеспокоенные конусностью, должны знать, что производители станков разработали новую технологию, которая улучшает качество и скорость резки, одновременно уменьшая конусность в более толстом материале. Например, новая технология сопел используется для направления режущего газа непосредственно к разрезу, а не для его распространения по материалу. Кроме того, модуляция луча используется для улучшения качества кромки реза.
№ 3: Помните о рельефе изгиба
Одним из лучших преимуществ использования лазера для обработки листового металла является то, что с его помощью можно создать практически любую необходимую форму. Единственным ограничением является размер детали, хотя просто удивительно, насколько маленькими могут быть детали, вырезанные лазером.
Одной из постоянных ошибок при проектировании деталей является неправильный рельеф изгиба, прорисованный в деталях.
Часто в тонком материале эти рельефы слишком тонкие, чтобы обеспечить хороший разрез прямо с помощью лазера. Проблема возникает потому, что вспомогательный газ движется по пути наименьшего сопротивления, который является первым сегментом пути, по которому проходит лазер.
Когда лазер движется обратно вверх по другой стороне рельефа, расплавленный материал не выбрасывается должным образом, что приводит к образованию окалины на краю рельефа.
Этот мусор мешает на повороте. Деталь необходимо перерисовать, чтобы лазер смог ее правильно обработать.
№ 4. Поставьте прокол на место
Прокалывание материала лазером значительно улучшилось по сравнению с тем, как оно работало в первые годы Производители теперь могут использовать различные методы прошивки для обработки своих деталей. Мягкий и многоступенчатый прожиг разработан таким образом, чтобы свести к минимуму количество брызг, которые могут попасть на готовую деталь.
Оптические датчики также используются для определения момента проникновения лазера в материал и начала резки. Эта особенность помогает сократить время изготовления деталей.
Поскольку внешний вид готовой детали часто имеет важное значение, лазерный программист должен разместить точку прожига в идеальном месте. Одно из лучших мест для прокола — середина небольшого куска материала. Размещение его там значительно снижает риск разбрызгивания и теплового эффекта в более толстом материале.
Что произойдет, если прокол окажется не в том месте? Рассмотрим прокол, расположенный на расстоянии 1/4 дюйма от края отверстия, расположенного на расстоянии 1/2 дюйма. мягкая сталь. Если точка прокола расположена близко к краю, который будет разрезаться, нагрев или брызги от прокола могут повлиять на качество резки или даже привести к ее потере. Отодвинув точку прожига от края, инженер-конструктор решает эти проблемы.
№ 5: Будут ли детали покрыты порошковой краской?
Если деталь должна быть покрыта порошковой краской, изготовитель должен помнить о нескольких вещах. Самый важный вопрос – какой вспомогательный газ следует использовать для резки. Если используется кислород, потребуется вторичный процесс, такой как галтовка или кислотная ванна, для удаления оксидного слоя, который образуется на кромке детали во время лазерной резки. Если этот оксид не удалить перед нанесением порошкового покрытия, отвержденное порошковое покрытие в конечном итоге отслоится, поскольку оно прикреплено к оксидному слою, а не к самому металлу.
Чтобы исключить необходимость удаления оксидного слоя, производители могут использовать азот в качестве вспомогательного газа, поскольку он обеспечивает чистый разрез. При резке азотом чем больше мощность лазера, тем толще материал, который он может обработать. Увеличение скорости сопровождается увеличением мощности. Оператор должен знать уровень мощности станка, чтобы знать максимальную толщину, которую можно аккуратно разрезать.
В зависимости от мощности лазера производителю также необходимо учитывать способность машины обрабатывать материал с желаемыми конечными результатами. Если, например, компания хочет приобрести лазер для чистой резки 0,1875 дюйма. сталь, которая будет иметь порошковое покрытие, компания хотела бы проанализировать различия в готовой детали при использовании станка для лазерной резки мощностью 3 кВт по сравнению с оборудованием мощностью 4 кВт. Более высокий уровень мощности машины мощностью 4 кВт может дать им результаты, которых они хотят достичь без азота. Для машины мощностью 3 кВт может потребоваться использование кислорода в качестве вспомогательного газа для лазера, чтобы получить деталь без окалины.
№ 6: Толщина материала больше не имеет значения
Станки для лазерной резки плоских листов действительно делают успехи в обработке материалов. Сегодняшняя технология твердотельной лазерной резки обрабатывает тонкие материалы очень быстро. Например, станок для твердотельной лазерной резки мощностью 8 кВт может резать сталь толщиной 0,039 дюйма со скоростью, превышающей 2000 дюймов в минуту (IPM).
Даже для толстых листов разработчики технологий производства продолжают увеличивать скорость резки. Используя новейшую технологию твердотельной резки, производители могут резать детали толщиной 1 дюйм. мягкой стали на скорости более 35 дюймов в минуту. Особенно для этого материала скорость улучшилась по сравнению с тем, что было возможно всего несколько лет назад. Качество реза также значительно улучшается.
Новейшая технология лазерной резки также позволяет обрабатывать детали размером до 1 дюйма. алюминий и 2-дюймовый. нержавеющая сталь Для отражающих материалов, таких как латунь и медь, эти лазеры могут резать толщиной до 0,38 дюйма без проблем с отражением луча.
Эта сборка, состоящая из материалов различной толщины, представляет возможности современной технологии твердотельной лазерной резки.
Конечно, это одни из максимально возможных толщин. В общем, по мере увеличения или уменьшения уровня мощности лазера увеличивается и максимальная толщина материалов, которые можно разрезать на станках.
№ 7. Форма детали влияет на эффективность резки.
Технология твердотельной лазерной резки увеличила скорость резки и надежность станков, но не изменила взгляды людей на проектирование деталей. Независимо от того, разрезаете ли вы традиционным лазером CO 2 или твердотельным лазером, производитель должен учитывать одни и те же соображения, чтобы повысить надежность процесса резки и получить наилучший конечный результат.
Например, если деталь спроектирована с углами под углом 90 градусов, время резки может увеличиться, а качество детали ухудшиться. Поскольку лазерная режущая головка должна замедляться при прохождении острого угла, она может пережечь углы, что приведет к образованию окалины. Это может даже полностью сжечь углы. Как правило, чем больший радиус может допустить инженер-конструктор, тем лучше. Это позволяет производителю увеличить скорость резки и качество детали.